Injection Molding Surface Finish
- Dominykas Turčinskas
- Sep 13, 2022
- 4 min read
How a product looks and feels can make a world of difference to its value. That’s why choosing the right surface finish for injection molded parts is crucial. However, a surface finish goes beyond aesthetics, as it can significantly impact a product’s usability.
In this article, you’ll learn about the different surface finish types and how to choose the right one. But first, we need to make an important distinction.

Tool Surface Finish vs. Texture
While often used interchangeably, surface finish and surface texture aren’t the same.
Finish refers to the general condition of the surface. Texture, on the other hand, is a quantitative characteristic of a material that encompasses three major determinants – lay, waviness, and roughness.
Think of texture as a sub-category of surface finish. In other words, surface finish includes the texture, along with other characteristics like coating (painting or anodizing). In practical terms, this means that you’ll use different processes for finishing and texturing.
Now that we’ve explained the terminology, let’s move on to the importance of a product’s surface finish.
Why You Should Use Different Finishes
As previously noted, surface finish impacts many of the product’s core characteristics. In retail, for example, the surface finish can make or break a product’s perceived value due to aesthetics. Plus, it can conceal some of the product’s imperfections like sink or line marks.
The surface finish also determines the product’s functionality to a certain degree. Many products require a user to have a firm grip on them for proper use, such as fitness equipment. In this case the finish should be slip resistant. Getting the finish wrong can be a costly mistake. To help you avoid that, let’s dive into various finish types.
Explaining Different Types of Finishes
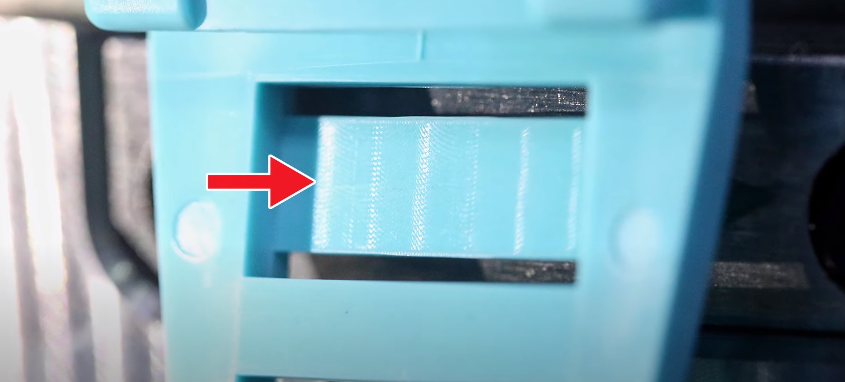
Mold manufacturers and designers must plan a product ahead to ensure that the surface finish suits its specifics and materials. To make this easier, the Society of the Plastics Industry (SPI) defined finish standards so everyone involved in the process can follow them. The standards encompass 12 different surface finish grades categorized into four groups (A, B, C, and D).
These categories describe the roughness of the finish and range from glossy and smooth to dull and rough finishes. It’s important to understand this classification as it provides guidelines on what surface finish to use with each material. For example, when working with ABS, it’s best to choose a finish ranging from B-3 to D-2. For acrylic, however, it’s best to use A-1 to A-3.
SPI is also important for determining the finish treatment method. For instance, C-1 to C-3 finishes are polished with fine stone powder. D-1 to D-3 use the same method, except they’re dry-blasted afterward.
SPI isn’t the only standard out there. You should also consider VDI (Verein Deutscher Ingenieure). It’s an international standard for matte surface texturing. VDI finishes are commonly treated using EDM (Electrical Discharge Machining), although traditional techniques like sandpaper or stone texturing are also applicable.
Finally, Mold-Tech (MT) specifications classify finishes according to texture depth and serial number. You can form MT finishes by chemical etching and laser-altering the mold cavity.
With many options to choose from, how do you know what finish you should use? Let’s look at how to select the right one.
What to Consider When Choosing a Finish?

There are a few factors that you should take into account when deciding on the surface finish. Here are some of the most impactful.
1. Injection Speed and Temperature
Generally, faster injection always provides a smoother and glossier surface, regardless of other parameters. Combine this with higher mold temperatures, and you’ll get a glossy SPI finish. Lower temperatures and injection speed may meet other requirements, but they won’t give such a smooth finish. By increasing the injection speed, you can also reduce the visibility of weld lines due to minimized fiber orientation.
2. Mold Choice
The mold you go with plays a critical role in the surface finish. You can make the mold out of various metals, although aluminum and steel are the most widely used. Even between these two materials, you can get very different finishes.
If you don’t need a highly smooth or glossy finish, an aluminum tool should do the trick. However, if a product calls for low roughness, it’s best to use a hardened steel tool.
3. Materials
There’s a wide range of materials used in injection molding. Each has specific properties that impact the finish regardless of the molding process and its parameters. For example, certain plastics are easier to smooth than others, and you need to know these characteristics to get the desired finish efficiently.
This is where it pays to remember the SPI specifications. To make things simpler, here’s a short compatibility list according to the SPI grade:
· Grade A – Acrylic, PC
· Grade B – Nylon, PP, Polystyrene, ABS, HDPE
· Grade C – Nylon, PP, Polystyrene, ABS, HDPE
· Grade D – Nylon, PP, Polystyrene, ABS, HDPE, TPU
It’s also crucial to remember the additive compounds that you’ll mix with the resin, as they can greatly change their properties. For example, carbon black reduces surface roughness, while fiberglass lowers gloss.
4. Functionality
Surface finish doesn’t just impact the end product’s functionality from the user’s perspective. It can also influence other manufacturing stages. Let’s say the product will be painted. In this case, you shouldn’t go with a smooth finish as doing so will make it harder for the paint to adhere properly. The same goes for adding labels – it takes some roughness to ensure it sticks. Therefore, always keep the end product in mind when choosing the finish.
Know Your Finishes
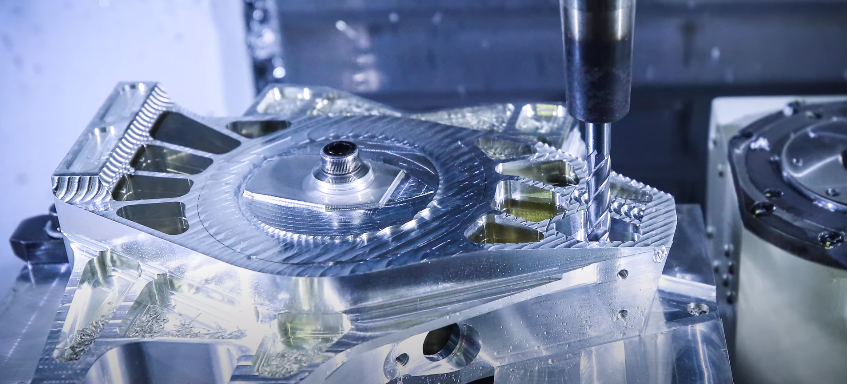
As you can see, choosing a finish is an important decision that involves quite a bit of critical thinking. If you haven’t already, it pays to familiarize yourself with the types and specifications mentioned here, as understanding them is crucial to choosing the right finish.
It’s best to decide on the finish early in the manufacturing process. As mentioned, surface finish impacts many other choices you’ll make in the later stages. Take some time to think about the finished product’s design and functionality, consider the molding process, and choose the finish that perfectly complements all of these factors.
Comments